Two years after their introduction at Fakuma 2012, sales of 5X Line 5-axis-servo robots from Sepro Robotique (La Roche Sur Yon, France) are taking off. As 2014 comes to a close, the company says it expects to sell more than twice as many 5-axis units this year compared to last year… nine times as many as in 2012. This makes the 5X Line the fastest growing, by far, of the five new product lines introduced by Sepro in the last two years.
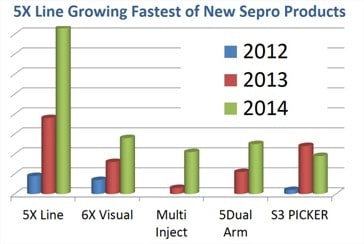
Jean-Michel Renaudeau, Sepro CEO, explains this remarkable record this way: “To be a successful molder today, you need to produce complex parts, on short cycles and with exceptional quality. You need to make frequent mold changes with as little downtime as possible. And you need to do all this economically with fewer skilled employees. Even molders who are not operating under these conditions today recognize that this is the direction the industry is moving and they are eager to invest in technology that they will need in the years to come. This is what is driving demand for 5-axis robots.”
Based a standard 3-axis Cartesian beam robot platform, the 5X Line adds a 2-axis servo-driven wrist developed in partnership Stäubli Robotics. Unlike pneumatic wrists, which can only move in a continuous arc from 0° to 90° or 0° to 180°, the 5X wrists can move from 0 to 180° and 0 to 270° or any part of those rotations with absolute precision. The servo motor has a positional encoder that recognizes exactly where the drive shaft is at any moment. Then the system control can integrate positional signals from all of the servo motors on all 5 axes so that it knows exactly where the gripper and part are in space at all times. This allows the robot to complete very complicated motions very precisely and with perfect repeatability.
Customers who have installed Sepro 5X Line robots in the last two years say that several specific capabilities helped them to make that choice:
- Accuracy in gripping and downstream positioning… Unlike a pneumatic wrist, the 5X servo wrist can grip parts at any angle and place them on conveyers or in sizing fixtures even in unusual orientations. End-of-arm tooling (EOAT) can be designed to accomplish the same thing, but it can be costly, time-consuming and can require frequent maintenance. With a servo wrist, the flexibility is easily achieved via programming.
- Adaptability to different molds and machines… Custom or trade molders often need to run tooling that they did not design, or run a given mold in any of several different molding machines to achieve scheduling efficiency. Accommodating subtle differences with pneumatic wrists and associated EOAT can be complicated and require mechanical adjustment by skilled employees. A servo wrist, on the other hand, can be easily adapted with simple digital commands.
- Multiple servo-driven motions… Whether it is needed to remove a complex part in a tight mold space, delicately position inserts at high speeds, or move the edge of a part past a flaming fixture, customers say that the ability for the wrist to make small, precise motions in synchronization the rest of the robot is extremely valuable.
- Clean operation… The wrist is driven by clean electric servo motors, making the 5X Line robots ideal for medical and other applications that cannot tolerate particulate (resulting from drive-belt wear, for instance) or lubricant contamination. The wrist module is completely enclosed.
- Reliable and repeatable… The digital accuracy of servo drive motors, which have positional feedback built in, has been proven over many years and they are essentially maintenance-free. In contrast, the speed and responsiveness of pneumatic units can be affected by air temperature, contamination or leaks, and frequent maintenance is required.
- Cartesian speed and simplicity… Many of the complex part-manipulation tasks mentioned above have historically been assigned to 6-axis articulated arm robots. Because it is a Cartesian or linear robot however, a 5X offers faster intervention into the mold space with multi-axis flexibility otherwise associated with an articulated unit. Set-up and operation are highly intuitive and programming was designed to fit the unique needs of injection molding.
The Stäubli wrist is a proven design that has been standardized and, Renaudeau notes, is becoming more affordable every day. “Of course,” he explains, “the 5X Line is a bit more expensive than our general-purpose Success robots or even the more technological S3 Line, on which the 5X robots are based. Our customers, however, look at it as a one-time investment that will continue to pay off in added productivity, quality and lower operating costs for years to come. In fact, many of the 5X Line robots we’ve sold are being used today in applications that could be performed quite easily by a one of our 3-axis robots. However, these customers are looking toward the future when they will require robots with more flexibility and more advanced part-handling capabilities. That’s why they are investing in these advanced robots today. It is also why we expect to see interest in 5-axis robots to continue to grow rapidly.”
The 5X Line of robots brings together a Sepro 3-axis Cartesian beam robots and a 2-axis Stäubli wrist is added to provide a total of 5 CNC axes of motion.