
Sepro Connect Dashboard
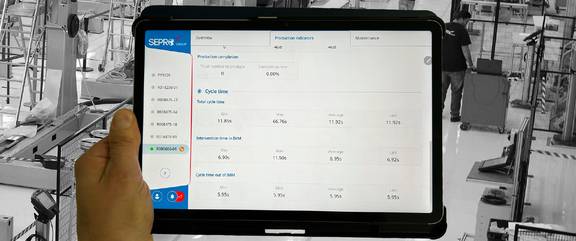
Sepro Connect Dashboard Helps Molders Optimize Operation of Automated Cells Plantwide
Seamlessly gathering data from all the equipment in automated plastic injection-molding cells – including the molding machines – the new Sepro Connect automation cell dashboard from Sepro Group promises to transform the way plastics-product manufacturers manage production, enhance overall productivity and control energy consumption.
The concept for the Sepro Connect dashboard was first seen at K 2022, where it gathered data from a single highly automated molding cell on the Sepro stand. Now, at the Fakuma 2023 trade fair (Messe Friedrichshafen, 17 to 21 October), Sepro engineers will demonstrate an expanded range of capabilities. These include the ability to gather and present information from multiple plastic molding cells in different locations. At Fakuma, the system will monitor equipment not only on the Sepro stand, but it will also gather data from robots running in the booths occupied by many IMM partner companies. The enhanced system also now can monitor energy consumption, helping businesses reduce their environmental footprint and operational costs.
A global leader in robotics for the plastics injection-molding sector, Sepro Group has also become known as an innovator in the broader field of industrial automation as applied to injection molding cells.
“We believe an automation specialist like Sepro is uniquely positioned to centralize data collection and analysis,” explains Charles de Forges, CEO of Sepro Group, “because our robots and the Visual control system already can communicate with almost any molding machine, regardless of brand, and can connect with peripheral equipment too. Other proprietary systems are not as open.
“We envision a system that is a sort of ‘data octopus,’” he continues, “reaching out to capture all production data from multiple cells… from the robots, of course, but also from the IMMs and all the peripheral equipment too. We are still only in the developmental phases today, but with centralized storage and analysis of all this data, we expect that very soon we will be able to give molders unprecedented power to optimize plant operations, increase productivity and reduce costs. ”Key features of the Sepro Connect dashboard being demonstrated at Fakuma include:
- Data Collection
The dashboard collects data seamlessly from production cells, providing real-time insights into production processes, energy consumption, and preventive maintenance needs. Data is collected from the robot controls, which are linked to the IMM so that its operating status, good/bad part production numbers, process data (times, temperatures, pressures, etc.) and IMM alarms are also collected. Wireless hardware tracks the operation of peripherals. Then, from almost anywhere, molders can log in to see an overview of all the connected cells, their working status, their production progress, scheduled maintenance, and energy consumption figures. Sepro takes data security seriously, so all data is stored in a secure cloud solution.
- Intelligent Alerts
An advanced alert system goes beyond traditional monitoring. The system compares quality, availability and productivity data to critical thresholds set up by the manufacturer. Deviation from key benchmarks generates alerts to allow the user to take proactive measures to prevent problems before they result in unnecessary downtime and production delays. Alerts are also generated when energy consumptions deviate from their targets.
- Productivity Enhancement
By harnessing the power of data analytics, the Sepro Connect dashboard empowers manufacturers to identify bottlenecks, inefficiencies, and areas for improvement. This data-driven approach streamlines operations and enhances overall productivity. Process engineers and maintenance personnel can take proactive measures when the Overall Equipment Effectiveness (OEE) ratio deviates from the target.
- Energy Optimization
Monitoring robot energy consumption and issuing alerts when it recognizes deviation from targeted energy consumption, the Sepro Connect dashboard can help businesses reduce their environmental footprint and operational costs. Predictive maintenance measures then can be taken to fulfill environmental-footprint targets. Eventually the system will be able to do the same for automated peripherals and even gather similar information from IMMs.
"Today's manufacturing landscape demands productivity, efficiency, and sustainability," Charles de Forges concludes. "The Sepro Connect dashboard is designed to empower manufacturers with the data and insights they need to excel in these areas, ultimately leading to greater success and competitiveness. The Sepro solution will be flexible and customizable according to each customer’s needs. Everything is accessible from a secured cloud either on a tablet, smartphone or computer."
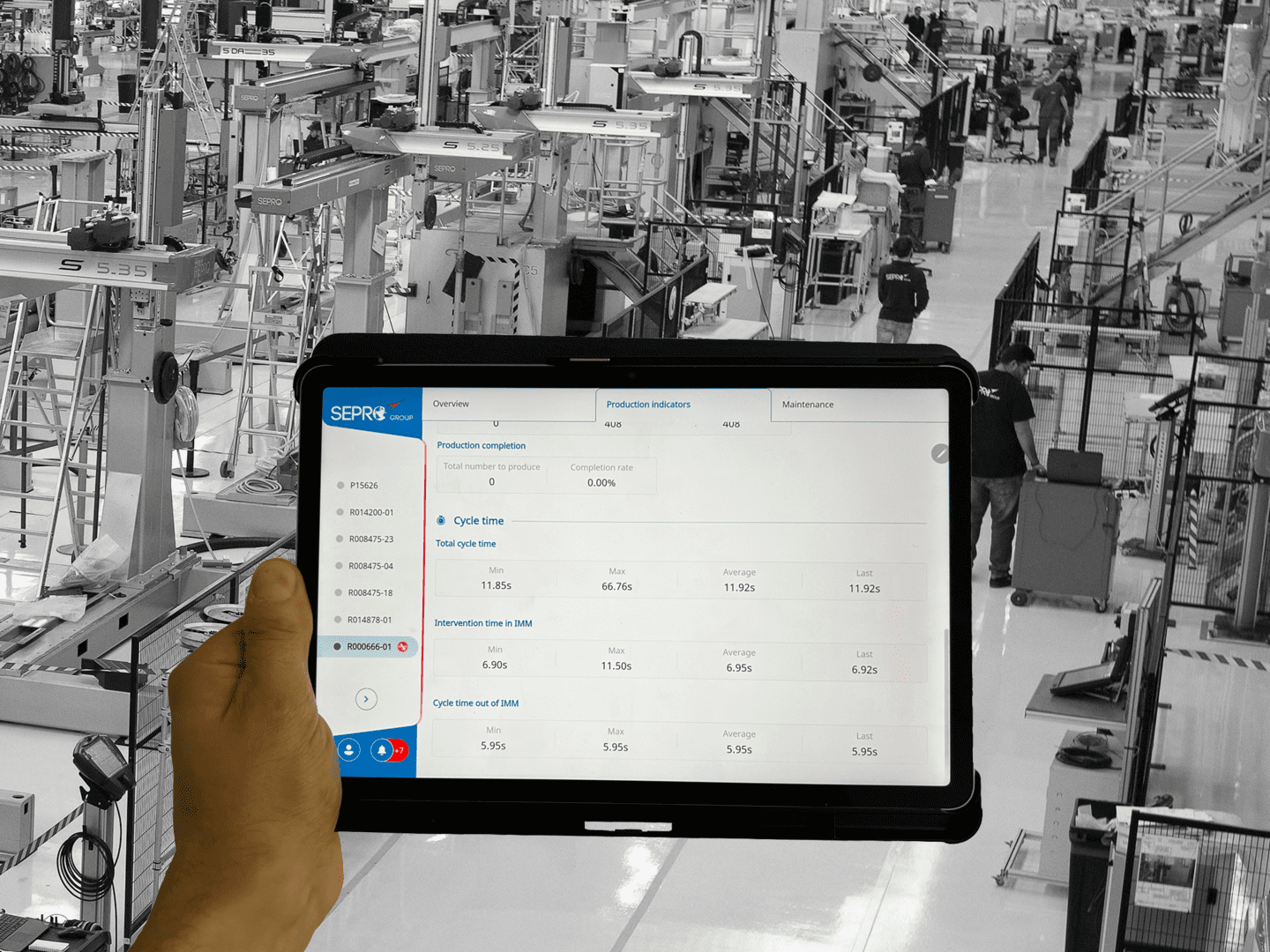
Stay connected
Receive a summary of our news and events every month