
Sepro innovation: The ThundeRbot
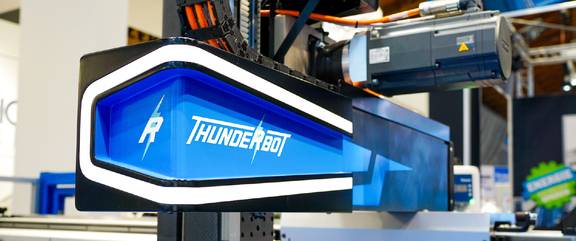
Sepro Design Innovations Enable ‘ThundeRbot’ to Reach Highest Speed
How would you redesign a general-purpose top-entry robot to make it as fast as possible?
This was the challenge undertaken by engineers at Sepro Group, the French robot and injection-molding automation supplier. The result of their efforts – the fastest top-entry robot Sepro has ever built -- can be seen in full-speed operation at Fakuma 2023, the plastics trade fair being held in Friedrichshafen, Germany, October 17 – 21. Sepro is exhibiting in Hall A1 on Stand 1203.
Starting with a standard Success 11 8U robot, the designers made modifications that resulted in a robot that requires just a fraction of a second to remove a plastic part from an injection mold. At Fakuma, the ThundeRbot, as it has been named, can be seen operating on a Demag molding machine producing small cups. The overall cycle time is just 3.07 seconds and mold-open time – during which the robot arm enters the mold, removes the part, and exits again – is a mere 0.79 seconds.
“We challenged our design team to implement every possible measure in order to increase speed,” explains Charles de Forge, CEO, Sepro Group. “So, what we are showing is a concept machine and, just as automakers use concept cars to introduce innovative new ideas, the ThundeRbot is Sepro’s attempt to demonstrate how our engineers innovate – think outside the box, if you will – to overcome challenges to achieve a specific objective.”
LOSING WEIGHT
The key to achieving fast cycle times is the robot’s vertical Z arm, which enters the mold space and removes the part. A new cycle cannot begin until the Z arm exits and the mold closes. Because the distances traveled are quite short, final speed actually is less important than acceleration.
On the ThundeRbot, the Z arm can accelerate at 80 m/s−2 (meter per second per second). That can be compared to 55m/s−2 on Sepro’s fastest robot (S5-25 Speed) and to 30m/s−2 for the standard Success robot. Thus, Thunderbot acceleration is 45% faster than that of the Speed robot and 2.6 times faster than Success.
Newton's second law of motion says the acceleration of an object is inversely proportional to its mass. A less massive (lighter) Z arm can accelerate faster than a heavier one, so the Sepro team focused on cutting its weight, eventually reducing it by roughly 6 kg (13.2 lb).
About half of the savings came by making moving Z-axis beams from a pultruded carbon-fiber-reinforced composite instead of aluminum, and linear guide rails are hollow. The end-of-arm tool (EOAT) used in the Fakuma demonstration, which is mounted at the bottom of the vertical arm to grip the molded part, is 3D printed. Air conduits to actuate the gripper are molded into the body of the tool, eliminating external tubing and fittings. The balance of the weight reduction was achieved by moving the electropneumatic components needed to operate the gripper and mounting them on the Y arm (strip axis) instead.
Once the weight of the Z arm was reduced, it was necessary to provide the structural stability needed to manage the increased speeds. So, the Y beam, which supports the Z arm, is made of carbon-fiber-wrapped aluminum for increased stiffness and to limit twisting. Finite-element modeling was used to optimize the X-beam spacer or riser (the mechanical interface between the robot and the IMM fixed platen) to increase rigidity. Inclined racks (with a tighter fit between teeth of the rack and pinion) improve drive-force transmission and reduce noise. The pinions themselves are self-lubricating, eliminating grease cartridges and reducing dripping. This innovation does not have an impact on speed, but it addresses customer concerns about maintenance simplicity and overall cleanliness.
Asked how these engineering innovations might influence design of robots in the future, François Bérot, Sepro CTO, commented: “It is pure speculation at this point but, from my point of view, the self-lubricated pinions, the optimized spacer and the inclined rack easily could be part of the next generation of Sepro robots. Carbon-fiber technology is probably too expensive to be considered today, but materials and processes are changing and improving constantly, so they might be more feasible in the longer-term future. In the meantime, we are working on other possibilities -- honeycomb structures, for instance – that could be used to reduce beam weight without compromising strength and rigidity.”
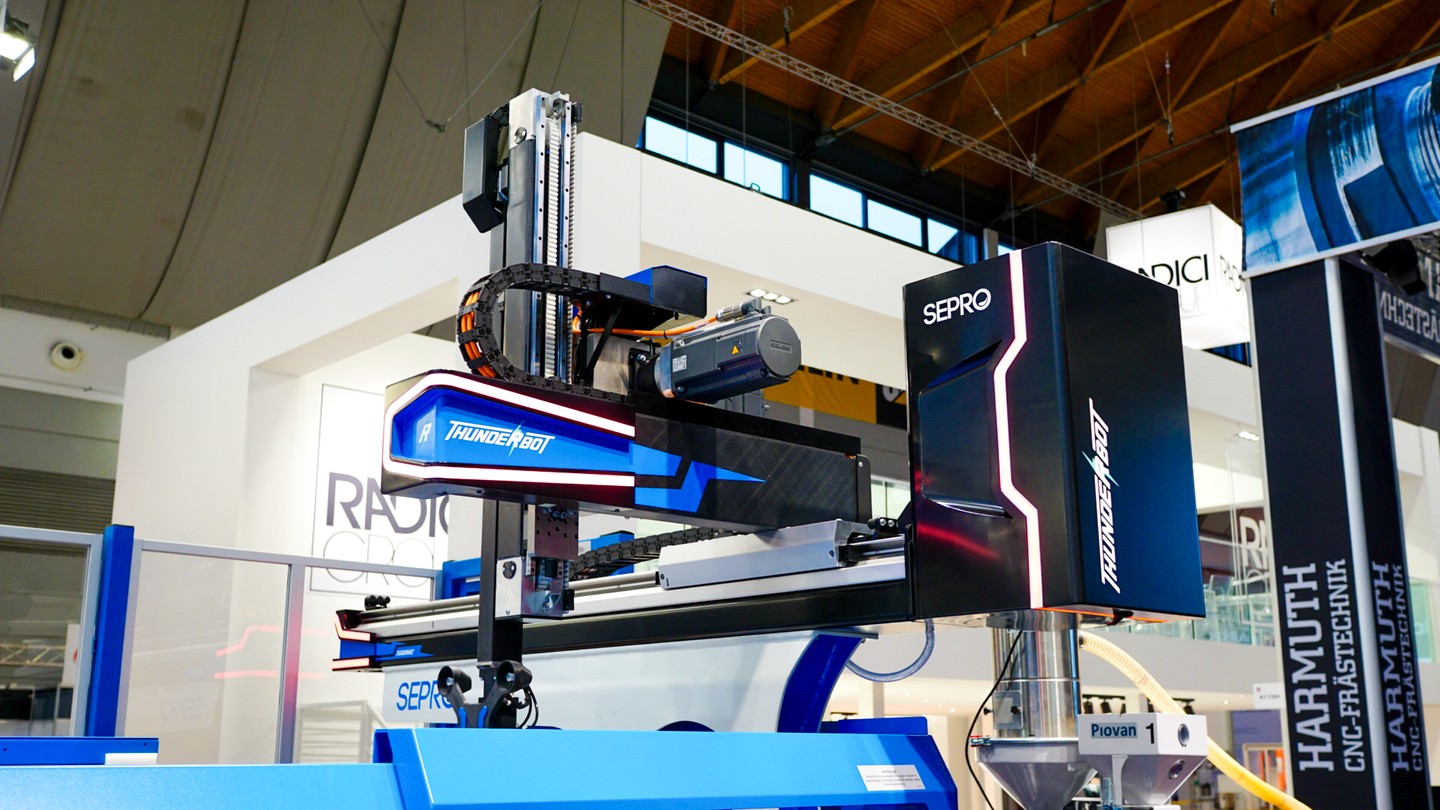
Stay connected
Receive a summary of our news and events every month